Medical Device manufacturing is a cornerstone of the modern healthcare system, providing innovative solutions that keep people moving.
From syringes and bandages to complex orthopedic implants and pacemakers, the industry is vast and continuously growing. The complexity of this sector stems from the rigorous standards and regulations governing the design, production, and distribution of products. Ensuring product safety and efficacy requires careful oversight at every step. From concept development to post-market surveillance, everyone has an impact on patient care.
From Concept to Commercialization
The development of medical devices is a detailed, multi-step process designed to ensure safety, quality, and effectiveness. It begins with conceptualizing an idea, followed by an analysis of its feasibility. Once the project is deemed viable, the development phase starts. This is focused on designing the device and testing its manufacturability. The next critical step involves qualification, ensuring that the device meets all necessary regulatory and safety requirements before commercialization.
In tandem, from a strategic business standpoint, the product’s market potential is evaluated and a project plan is established. This plan outlines each phase of development, including design, process validation, and regulatory approval. Once the plan is approved, engineering begins scaling the manufacturing process to meet market demand. Just like in the development phase, this stage will require a series of equipment/process validations and commissioning. The final step is to launch the product, marking the completion of its manufacturing development. However, continuous monitoring and improvements will follow throughout every products lifecycle.
Medical devices, whether small-scale or large, go through a series of iterations as they are refined and enhanced to meet the evolving needs of healthcare providers and patients as well as regulatory standards. Throughout the manufacturing process, every device is subject to rigorous testing to confirm it’s adhering to the approved design specifications.
Diversity Among Devices
Medical devices come in many forms and sizes, from simple instruments to highly sophisticated machines. On top of that, they also are segmented across various classes, ranging from low to high risk (Class I – III). This diversity makes the industry unique because each device may have to adhere to a different set of standards that are based upon the same overall principles.
Devices like stylets and pacemakers, although small, are indispensable in medical procedures. They have key similarities and differences that impact their “Class”. Stylets, which are thin and flexible wires (straws), are used in surgical settings to guide medical instruments such as catheters and ET tubes into the body. Pacemakers, on the other hand, are implanted to regulate the heart’s rhythm, which play an important role in saving the lives of patients with heart conditions. Both the Stylet and Pacemaker are small, enter the body, and crucial to a patient’s life, but are classified differently due to the level of control needed to ensure safety and effectiveness.
In addition to small-scale devices, large diagnostic machines like MRI machines and X-rays are critical to modern healthcare. MRI scanners use magnets and radio waves to produce detailed images of the body’s internal structures, which is valuable for diagnosing conditions such as cancer, neurological disorders and torn ACL’s. Whereas X-ray machines are vital for diagnosing bone-related conditions and infections such as pneumonia. Both of these large scale machines are similar due to the fact they take images of the body for diagnostic measures that allow the healthcare team to create individualized care plans. They are both class II devices, but they vary greatly in the type of images they can take.
Overall, these two examples show the innovation within the medical device industry and how similar and different every device is. There is one thing every medical device has in common, and that is their profound impact on patient care.
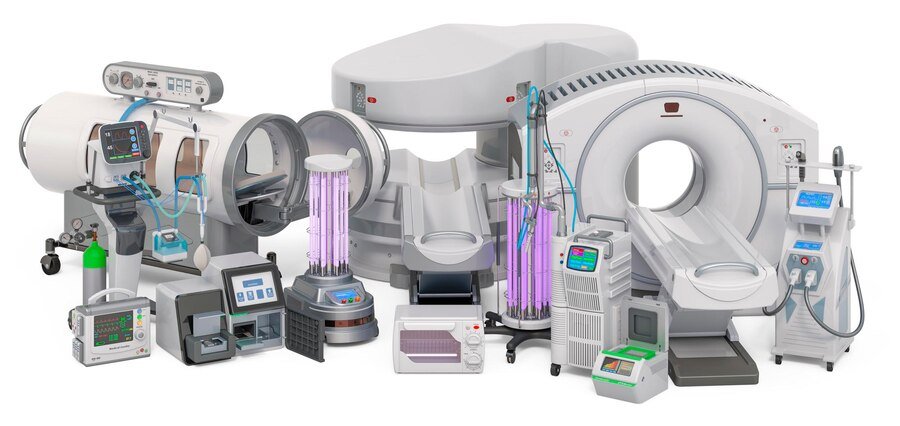
Adhering to Quality & Regulatory at Every Step
Upholding and ensuring a high standard of quality is paramount in medical device manufacturing. Quality Assurance (QA) processes are integrated throughout the production lifecycle to guarantee that each device meets the validated safety and performance standards. This involves extensive testing, inspection, and documentation (cGDP), beginning with the design phase and continuing through to final product release.
By adhering to rigorous QA protocols, manufacturers can identify and resolve potential issues early in the process, minimizing the risk of defective products reaching the market. QA is not only about meeting regulatory requirements but also guarantees that the medical devices consistently perform at the highest levels, fostering trust and reliability in the healthcare system.
In addition to quality, each manufacturer much ensure compliance with regulatory. This is essential for ensuring that products are both safe and effective. The FDA (Food and Drug Administration) plays a large role in this process by evaluating medical devices before they can be marketed to healthcare providers and patients. Manufacturers must demonstrate that their products meet stringent design, manufacturing, and clinical standards through a series thorough audits. In addition to the FDA, other regulatory bodies will conduct their own audits of medical device manufacturers to ensure their standards are being met.
These compliance process’ require companies to adhere to strict guidelines in areas such as device labeling, testing, and post-market surveillance. Manufacturers who meet the regulatory requirements not only ensure the safety and quality of their products but build a strong rapport between healthcare professionals and patients.
Custom Manufacturing and OEM Partnerships
Custom manufacturing and partnerships with OEMs (Original Equipment Manufacturers) are vital in the medical device sector. The custom manufacturers design, development and create specialized devices tailored to specific medical conditions or procedures. This approach confirms optimal performance and enhances patient care by providing the exact tools needed for complex procedures. The OEMs play a crucial role in providing the specialized components that meet the exact specifications required by medical device manufacturers. Whether it’s sensors for pacemakers or magnets for MRI machines, the OEMs supply essential parts that ensure the functionality and reliability of all medical devices. Through these collaborations, manufacturers can access cutting-edge materials, technologies, and expertise to develop innovative solutions that improve healthcare outcomes.
How We Can Help
With its extensive network of experts, KeyPoint Staffing offers comprehensive support for medical device manufacturers throughout every product phase. As technology advances, partnerships with OEMs and custom manufacturing will continue to play a critical role in developing specialized solutions tailored to patient needs. From engineering, regulatory compliance, quality assurance and technical sales, KeyPoint Staffing’s consultants bring specialized knowledge to help navigate the complexities of the industry and drive business growth/innovation, with a mission to advance healthcare worldwide.